「勘コツ」に頼る技術継承からデータドリブンの意思決定へ
名張工場から世界へ!DX企業アーケムの挑戦
株式会社アーケム様
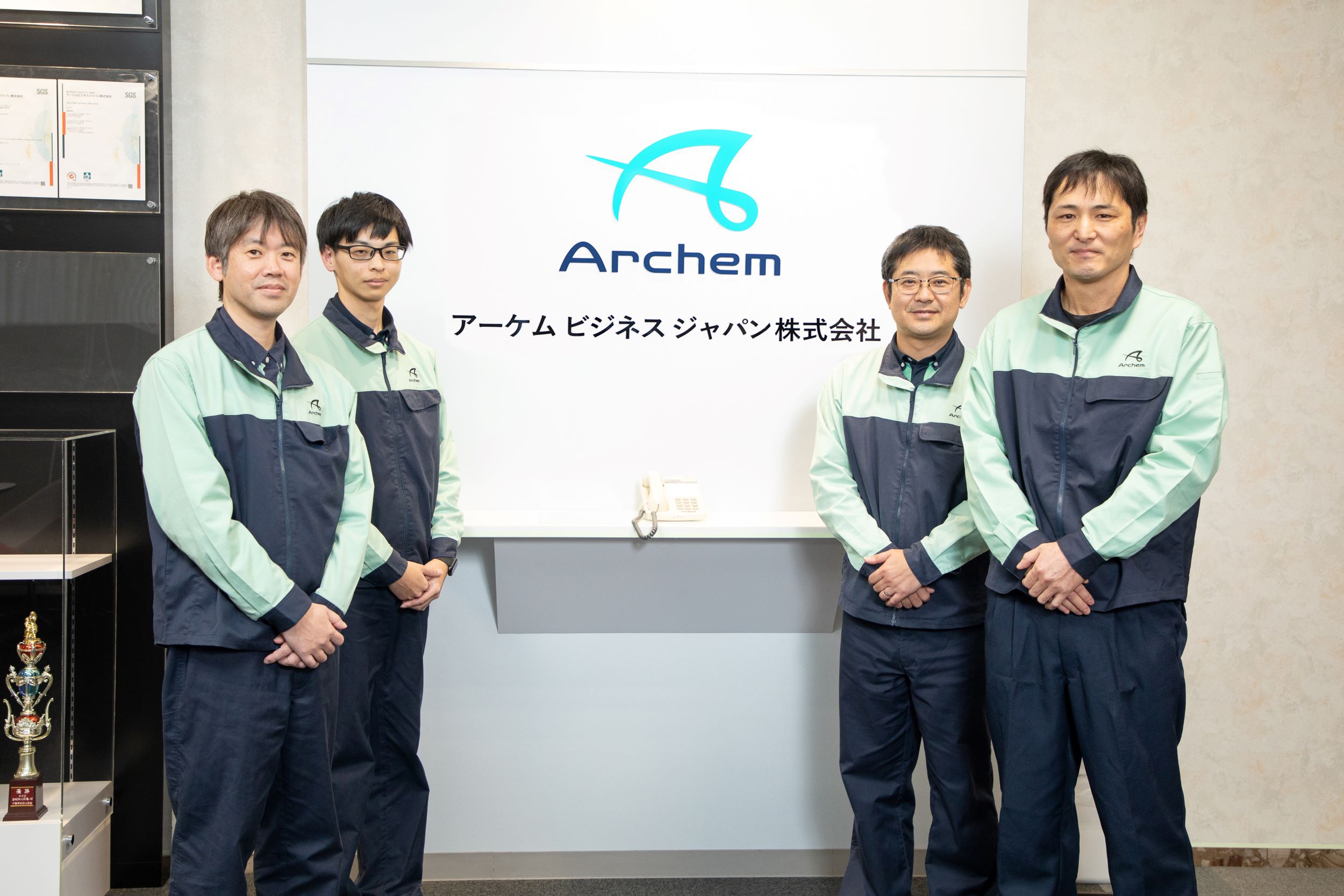
目次
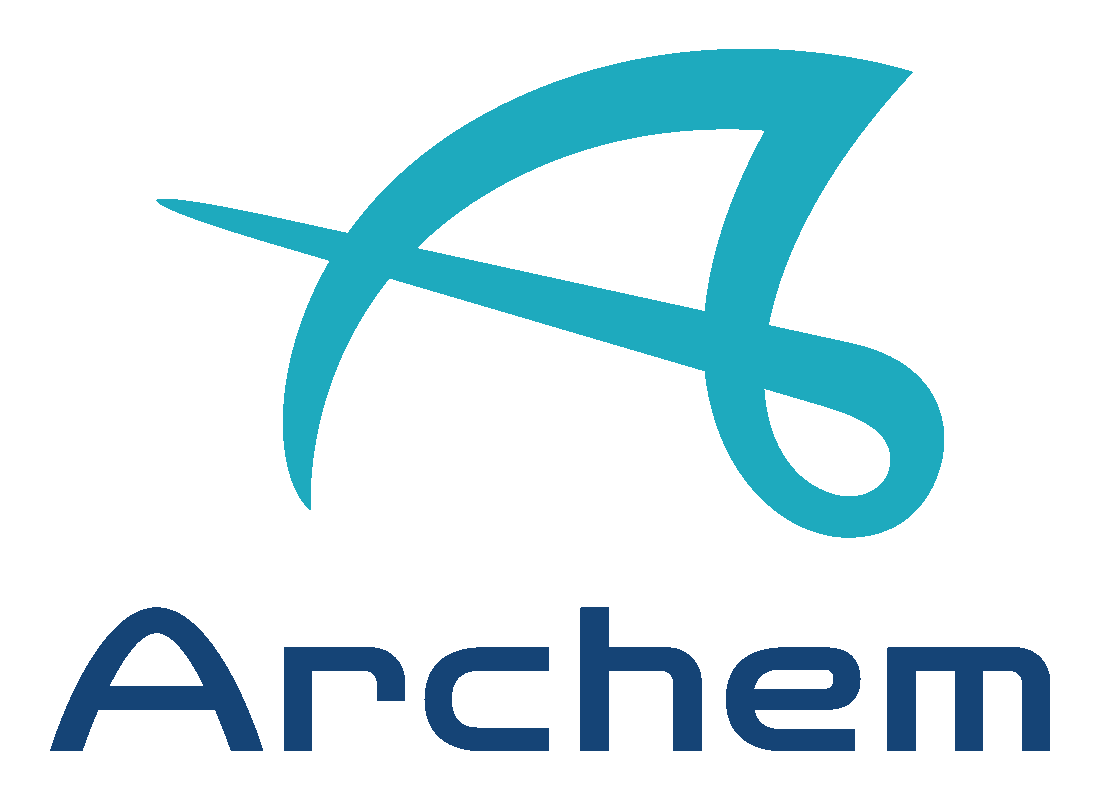
株式会社アーケム様
株式会社ブリヂストンの化成品ソリューション事業を前身として2022年に設立。「世界中のあらゆる場面に快適さを広げる」をビジョンとし、70年以上培ったウレタン技術と提案力で、お客様と社会のニーズに応えていくことを強みとしています。主要な事業はシートパッド事業、産業用化成品事業、事務機器用精密部品事業の3つ。ウレタン業界でNo.1を目指すべく、DXにより技術力と提案力をさらに高めるとともに、環境問題など社会にも貢献する方法を常に模索しています。
自動車シートに装着されるシートパッドや、ベッドのマットレス、まくらなど、私たちの身の回りの製品に広く活用されているウレタンフォーム。その製造に比類なき経験と技術を有するのが株式会社アーケムです。ブリヂストンの化成品ソリューション事業部から独立したのが2022年。新たな会社として出発すると同時に与えられたミッションが、製造現場のIoT化でした。手探りでのスタートの中、パートナーとして選ばれたのがDTS。
今回は名張工場でのPasteriot.miの導入にまつわる背景とこれまでの成果、そして名張から世界へと広がる今後の挑戦についてお伺いしました。。今回は名張工場でのPasteriot.miの導入にまつわる背景とこれまでの成果、そして名張から世界へと広がる今後の挑戦についてお伺いしました。
株式会社アーケム
淺田 拳吏 様 (シートパッド事業第一本部 本部長)
根本 真悟 様 (シートパッド事業技術部 シートパッド事業技術課)
稲垣 儀彦 様 (スラブ技術部 スラブ技術課 課長)
福本 優 様 (スラブ技術部 スラブ技術課)
宮末 研太郎 様 (生産統括部 生産・技術統括管理課 課長)
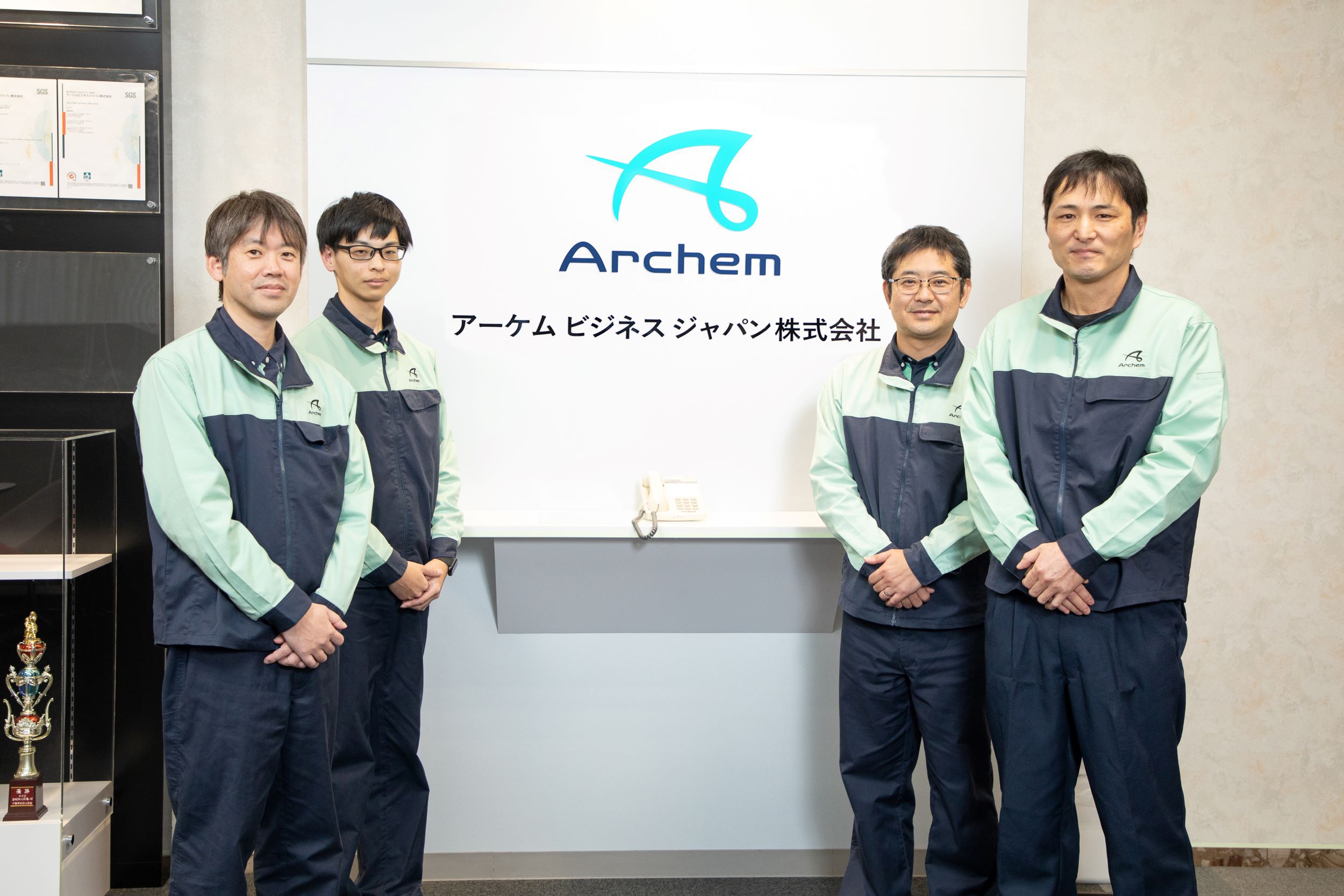
【導入の背景と選定の理由】 まさに工場の現場が求めていたソリューションだった
最初はどのような経緯でDTSにお声がけいただいたのでしょう?
宮末様:
アーケムとして新たなスタートを切るにあたり、経営陣から与えられた大きなミッションのひとつがDXの強化でした。新会社のITチームも発足したばかりだったので、まずは展示会を訪れてヒントを探していたのです。そこで出会ったのがDTSさんでした。DTSさんもちょうどPasteriot.miリリース直前のタイミングで、お互いにこれから!という時期でしたね。
他にも出展社はいらっしゃったと思うのですが、DTSのPasteriot.miを選定いただいた決め手は何でしたか?
宮末様:
IoT化や分析といったサービスを提供している会社はたくさんありました。しかし、多くはIoT化と可視化のみ、又は分析のみといったところが多く、一気通貫でお願いできるところは限られていました。
また、Pasteriot.miはAI分析の活用によって、特別な知識がなくとも使う事が出来る、ユーザーフレンドリーなサービスであったことも魅力でした。特に分析モデルの自動生成には興味を惹かれました。分析というとアカデミックなイメージがありましたが、これなら工場の現場でも活用できると感じたのです。まさに求めていたソリューションでした。
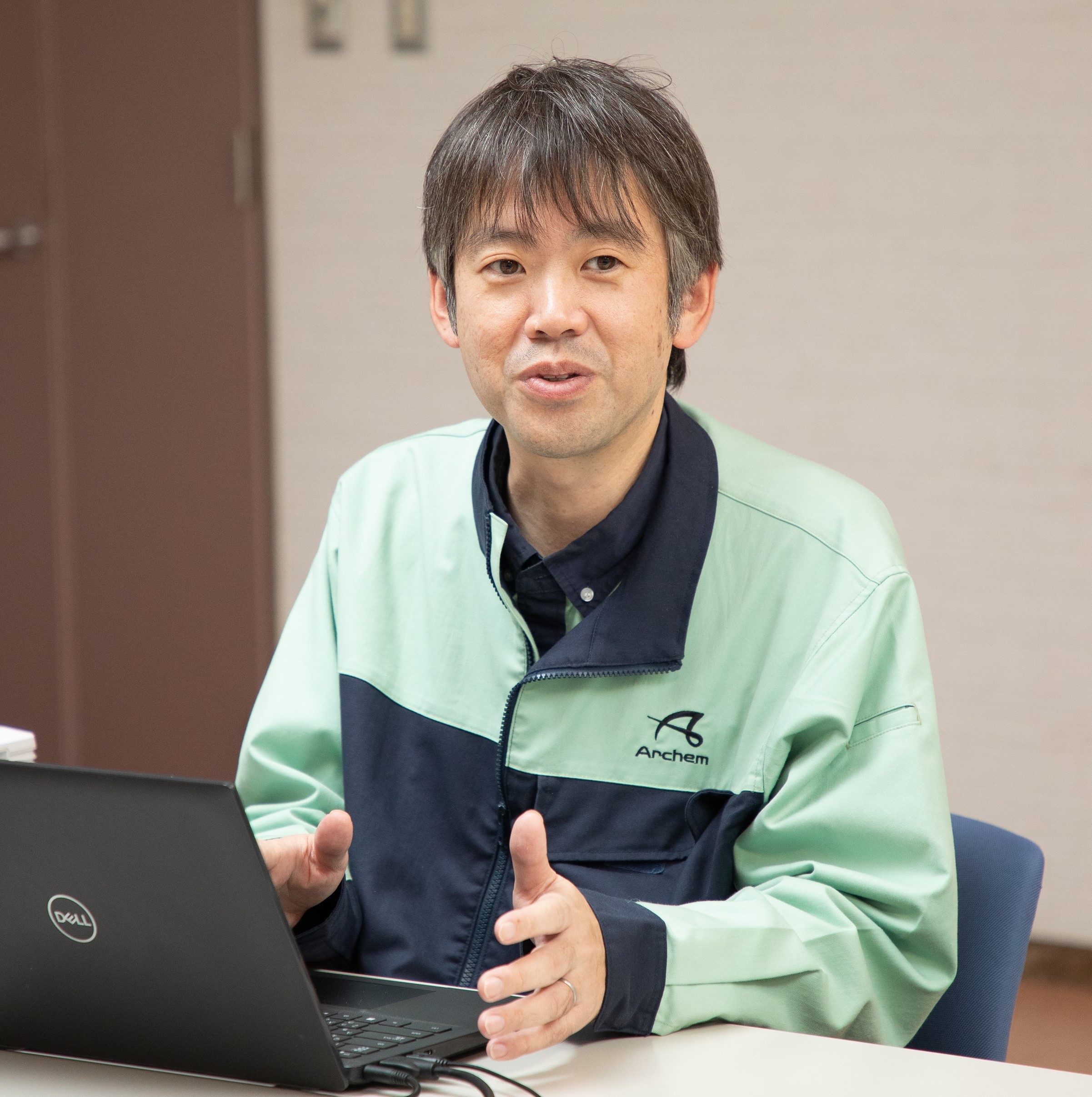
主要事業であるシートパッド、スラブというふたつの事業でPasteriot.miを導入いただきました。それぞれ当時の課題を教えていただけますか?
根本様:
シートパッド事業においては、不具合が発生した製品が、どのような製造条件で生産されたのか?など、品質問題の原因を追究しきれていない、という課題がありました。ロギングはしていたのですが、データをまとめて分析するところまで手が回らなくて。分析しようとすると、ひとりの専任者がひとつの分析テーマに1週間かかりっきりになってしまう状況で、大量のデータがたまるばかりでした。
またシートパッドの場合、製造中の情報、外観検査の情報、と情報が分断されていることに加え、ひとつひとつの製品がいつ製造されたのか?といった詳細情報までは把握できていませんでした。そのため、現場のデータと結果を紐づけて分析することに難しさを感じていました。
福本様:
スラブウレタンというのは、ポリオールとイソシアネートを反応させて硬化させた大きな食パン形状のブロックのことです。ブロックを切り取って、マットレスやまくら、様々な形状の製品に加工していきます。何種類もの原料をレシピ通りに調合して作るのですが、温度や湿度によっても仕上がりにバラつきがありました。うまくいかないと、膨らまない、ひびが入って割れる、といった不良品が生まれます。そうすると、ウレタンは再利用が難しいということもあり、この巨大な製品を廃棄するしかなくなります。この廃棄ロスを削減することが大きな課題でした。
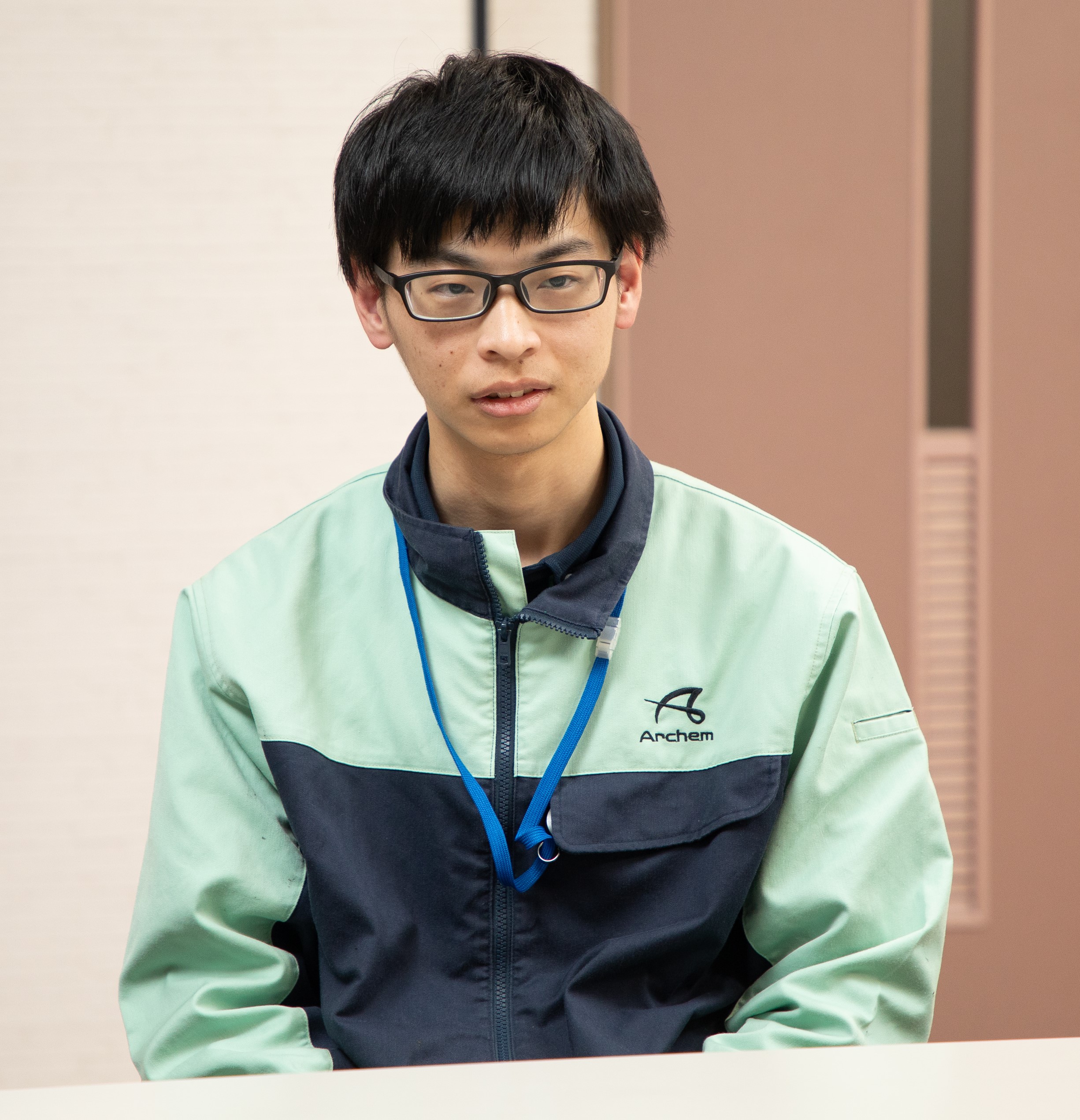
そのためには、人の「勘コツ」で調整していた作業をデータで分析したいという思いがありました。一部の製造ラインにはセンサーを取り付けていましたが、あくまでも目視・点検用で、データを取り込めていない状況でした。またスラブ工程は、機械を動かす速度など人手で調整することも多かったので、そこにも問題意識がありました。
【導入の過程】 度重なる変更にも柔軟な対応。技術者のITスキルもレベルアップ
会社も設立されたばかりの時期に進められたプロジェクトということで、ご苦労もあったのではないでしょうか?
宮末様:
そうですね。会社も部署もできたばかりで、IT方針も定まっていない状態でした。これまで使っていたブリヂストンのネットワークから切り離す必要があり、それと同時に今回のシステムも導入しなければならない。IT分野に強いメンバーも少ない中、プロジェクトを進めなければなりませんでした。まずはやってみて、変更を加え、また進む。その繰り返しでした。
例えば、DTSさんからの当初のご提案は、SnowflakeとDataSpider、そしてPasteriot.miを活用したものだったのですが、弊社は既存のソリューション(RedShift、Alteryx)を活用しており、共通のソリューションを活用したいというIT方針をプロジェクトで後から把握し、対応をご相談したこともありました。この時もDTSさんは柔軟に対応してくださり、結局既存のソリューションとPasteriot.miを連携する形で、社内のIT方針に沿うようにまとめてくださいました。
根本様:
最初は全てのデータをクラウドで処理しようとしていましたが、シートパッドのデータ量・情報量は特に多いためコスト面を含めて再検討することになって。一旦オンプレで処理してからクラウドに上げよう、という方針に変わったこともありましたね。
そのような困難をどのように乗り越えられたのでしょうか?
宮末様:
DTSさんには名張の工場にも何度か足をお運びいただき、定例の会議もかなり頻繁に行いました。その中で、ITに詳しくない私たちなりに希望をお伝えするのですが、それならこういう方法がありますよ、といつも分かりやすくご提案いただきました。DTSさんにお任せしていれば必ず実現する、という信頼感がありましたね。
また、Pasteriot.miは簡単に操作できる部分もありますが、使いこなすのが難しい機能もあります。ここに関しても、DTSさんと社内のIT部門とが時間をかけてコミュニケーションをとり、少しずつ理解を深めていきました。
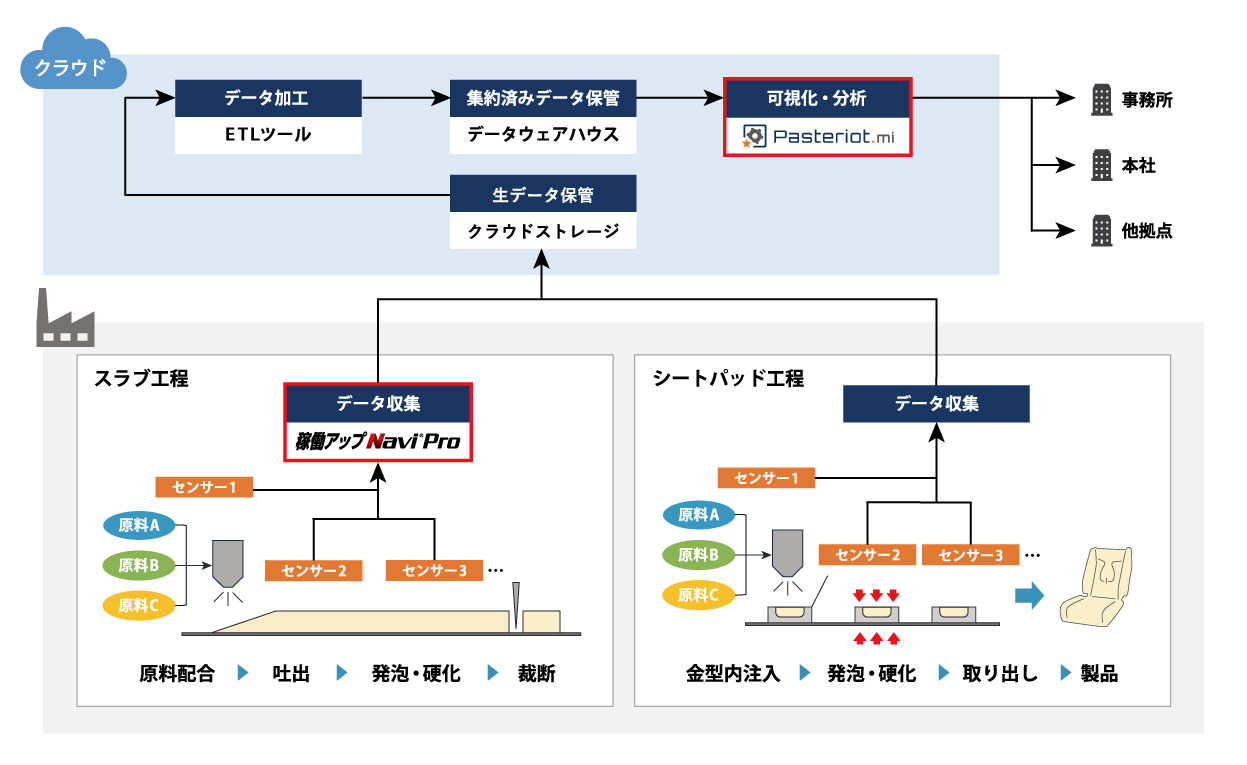
【導入の効果】 データを元にした議論が飛び交うように
製造現場にPasteriot.miが導入され、実際に使用されたご感想はいかがですか?
根本様:
ITの専門家ではない製造現場の私たちが、日々の業務をこなしながら操作方法を一から学び、大量のデータを扱うことになったので最初は大変でした。しかしそのおかげで、生産した製品の品質やそのバラつきを、細かく見ることができるようになったと感じています。特に製品の硬度と外観にバラつきが出るという課題があり、当時はその原因が分からなかったのですが、Pasteriot.miによって要因が明確化し、改善の糸口がつかめるようになったと思います。
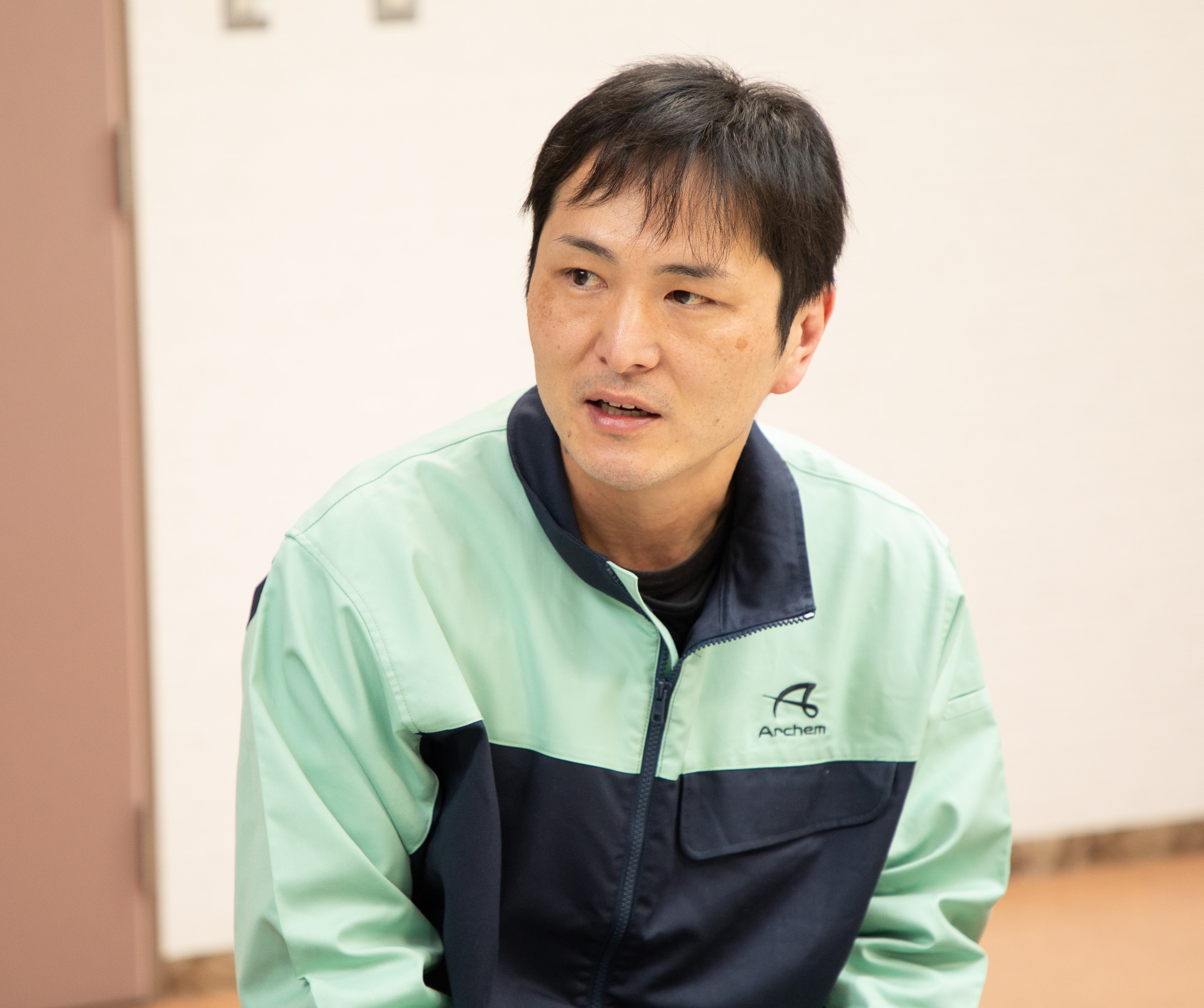
淺田様:
シートパッドの現場では、以前はデータ分析の専任も少なく、データを上手く活用できていませんでした。Pasteriot.miを導入したことにより、今ではデータを見ながら、技術者が集まって盛り上がる場面も見られます。分析に役立っていることに加え、技術者のレベルアップに繋がっているのではないか?と期待しています。
福本様:
データを元に議論ができるようになったのは大きな変化です。ここのデータがいつもと違うから、ここを変えたら?という仮説も立てやすくなりました。過去のロットにも遡り、変化点を探し出せるのも便利ですね。大きな課題である廃棄ロス減少のためのヒントも見えてきました。
稲垣様:
スラブの硬度や密度は温度や湿度によっても影響を受けるのですが、製造現場では数日先の天気予報を見て様々な条件を調整し、品質のバラつきを抑えています。データを見ながら未来よりも先に動く—これが可能になったのはPasteriot.miのおかげですね。
伴走支援のサービスもご利用いただきました。具体的にはどのような内容でしたか?
宮末様:
複雑なデータや形式を整理整頓して、Pasteriot.miをより使いやすく、そして分析の精度を上げるために様々なアドバイスをいただきました。可視化して有効活用するためのデータの準備にも対応いただきました。常に私たちの立場に立って、製造現場の技術者が分かるようにかみ砕いて説明いただき、そのおかげでデータを活用できるようになってきたと思います。
実際に分析してみて初めて、こうすればよかった!こんな情報も欲しかった!ということも多いですね。それに対しても、DTSさんが都度軌道修正してくださり、今でもアップデートし続けている感じです。引き続き伴走支援を受けながら、データを活用していきたいです。
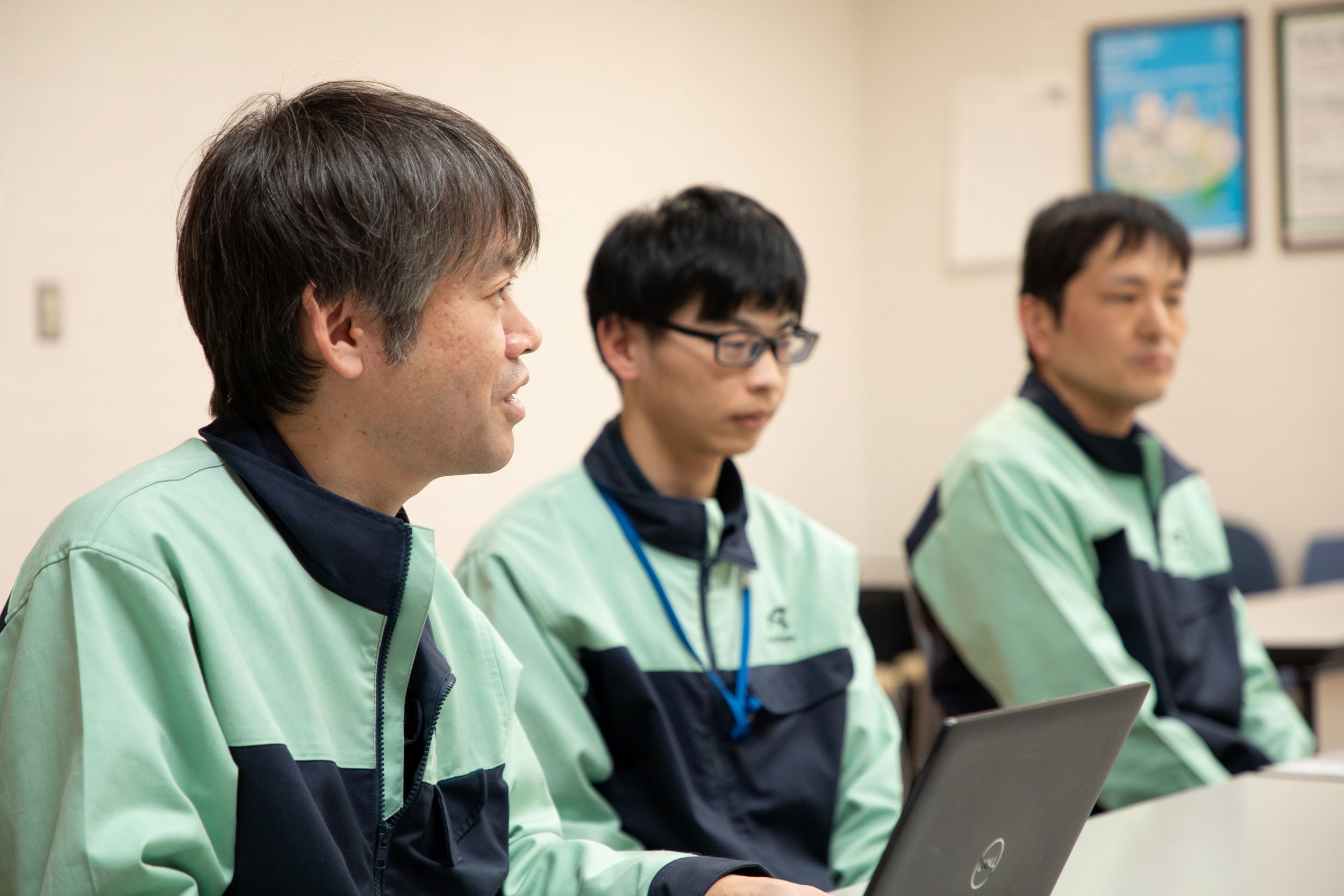
仕事の取り組み方も変わってきているようですが、社内での評価はいかがですか?
宮末様:
今回のプロジェクトは、海外含め、他の拠点にも紹介しています。DXの活用という、新しくてワクワクする話題ですから、技術者も聞きたがります。特にシートパッドについては興味が高いですね。名張工場発信で、各拠点の問題解決に貢献していきたいので、そのためにもまず名張で確実に効果を出し、名張で発見した問題解決のヒントは他拠点とも共有していきたいと思います。
経営層からも、データを活用して問題解決に取り組んでいるという点で評価を受けました。さらにリアルタイム性を追求し、予兆が出たらすぐに不具合の対策をできないか?という新たな期待も加わり、まだまだプロジェクトは続きそうです!
お取引先のお客様に対してはいかがでしょうか?
根本様:
品質が不安定だと不良品流出のリスクがありますが、原因が分かれば不具合は出ない。高品質の製品を安定的にご提供できること、そして万が一品質に不具合があった際にトレーサビリティが確立していることも、お客様からのニーズも満たすことになるのでは、と思います。
【今後の展望】名張の挑戦を全国へ、そして世界へ。環境問題にも応えていきたい
今後はPasteriot.miなどのDMSをどのように活用していきたいですか?
宮末様:
5年後、10年後には、新商品のスピード、改善のスピード、全てのスピードがさらに加速しているでしょう。これに対応するためには、データの活用がますます重要になります。弊社でも引き続きデータを活用しながら、それを問題解決に結びつけていけるよう、Pasteriot.miは技術者の教育ツールとしても活用していく予定です。そして、高い技術力に加えデータにも強いデータサイエンティストを、他の拠点にも増やしていきたいですね。現在名張工場だけで実施していますが、国内そして海外の他の拠点にもDXの取り組みを広げていきたいです。
御社は環境問題にも熱心に取り組んでいらっしゃいます。DMSが環境のためにできることはあるでしょうか?
稲垣様:
スラブ事業で大きな課題である廃棄ロスは、Pasteriot.mi導入によって問題解決の糸口が見えてきました。これは環境問題に対する取り組みとしても大きな一歩です。確実に成果を出すべく、データの力を借りて引き続き追及していきたいと思います。
また、弊社の環境に対する取り組みとして、植物由来製品の開発、そして不良品をウレタン原料に戻して再利用するというリサイクルの試みもあります。これに関しても、データを活用し可視化することで、よりスピーディーに推進していくことができるのでは、と考えています。
名張発の工場DXが世界へと広がり、ウレタン業界全体をもインスパイアする。そんな可能性を秘めたアーケム様のプロジェクト、今後の進展が楽しみです。本日はありがとうございました。