在庫管理と売上管理をリアルタイムに可視化。
生産計画のコントロールと需要変化の把握を支援する「GalleriaSolo」
中央発條株式会社 様
中央発條株式会社 様は「GalleriaSolo(ガレリアソロ)」を導入されました。導入された背景、選定のポイント、現在の運用と評価、今後の展望について伺いましたのでご紹介します。
業種 | 製造業(自動車部品) |
導入製品 |
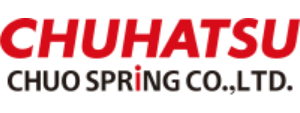
自動車用バネの大手メーカーである中央発條株式会社(以下、中央発條)は、主に在庫管理と売上管理の2つの業務領域でGalleriaSolo を活用。毎朝在庫数をカウントする運用をQRコードでの管理に変える取組みを実施中。日々の必要量と在庫量の対比を現場で可視化し、生産計画をコントロールする。また売上管理では、得意先別・品番別の日次売上を営業担当者全員が確認することで、品種ごとの需要の変化を細かく意識するようになったという。
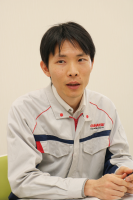
中央発條株式会社
システム企画室 IT化推進G
グループリーダー
想厨子 大吾 氏
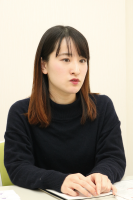
中央発條株式会社
システム企画室
IT化推進G
森田 夏紀 氏
導入の背景
Excelを印刷し紙で張り出す運用を見直し 最新のデジタルサイネージを導入
中央発條は、70年以上の歴史で培ってきた軽量化技術や材料・工法のノウハウなどで他社との差別化を図っているほか、トヨタ系列の会社として生産量の変動に柔軟に対応するスリムでコンパクトな生産ラインも独自に開発している。数年前からは、BIとダッシュボードを活用したデータの見える化にも取り組んでいる。
同社はIBM Power Systems(Power Systems)上のIBM Db2データベース(以下、Db2)とOracle Databaseを併用している。経営分析に必要なデータはシステム企画室が抽出して各部署が活用してきたが、データを分かりやすい形で見せる仕組みがこれまではなかった。そのため、ユーザー部門に大きな負担がかかっていた。例えば、朝8時の会議に使用する資料作りのため、早朝にCSVデータを抽出し、Excelでグラフ化する作業を繰り返すことも多かったという。
手作業でグラフ化する業務を自動化し、データベースの値が変化したら手元のグラフも変化するようなリアルタイムな可視化の仕組みがダッシュボードで実現できれば、会議用資料はもちろん、経営分析にも大きな前進になると考えた。
BIダッシュボードの選定にあたってはいくつかの条件があった。1つ目はPower Systemsから直接データを抽出できる親和性と投資効果の高さ。2つ目はデータ分析の専門知識がなくても扱える容易な操作性。そして3つ目はデータ活用のガバナンスが確保できること。中央発條 システム企画室 IT化推進Gグループリーダー 想厨子 大吾氏は、「汎用機時代はシステム企画室でデータ抽出し、その後は各部署で分析する運用を行っていましたが、社内に異なったデータが散在し、管理が困難になったことがありました。その反省から、データを渡す段階でシステム企画側である程度分析しやすく作り込んだ状態にし、データ活用のガバナンスを維持したかったのです。そうすればデータの一元化を実現できると考えました」と説明する。
選定ポイント
これまで見えなかったものを見える化し 労力をかけていた見える化も簡単に実現
BIダッシュボードには、Power Systems を提供するパートナー企業から紹介された、DTSの「GalleriaSolo」が選ばれた。Power Systemsとの連携性の高さはもちろん、ダッシュボード製品としては低コストで、システム企画室の担当者でも作り込める容易性が選定の決め手となった。
同社は2018年後半から試験運用を開始。「最初は工場の生産管理業務で使い始めました。当時、製造現場では納期が逼迫する状況がたびたび発生していたため、GalleriaSoloで納期別にどのような注文が入っているのかをグラフで可視化し、工場の片隅のモニターで表示したところ、ひと目で今抱えている納期ごとのバックオーダーを確認できるようになり、必要な製品のタイムリーな生産にシフトするための気付きにつながりました」と想厨子氏は振り返る。
その後は、生産管理部門での在庫管理と、営業部門での売上管理の2つの業務領域で本格運用に入った。
「在庫管理では、藤岡工場(愛知県豊田市)の自動車部品の製造ラインを対象に、日々の必要量と在庫量の対比を、現場の大画面モニターに常時グラフで表示し、在庫の少ない品番は点滅のアラートで表示するようにしています。生産管理部がその情報を参考に生産計画をコントロールしていますが、10分に1度自動更新されるので、ほぼリアルタイムに状況を確認することが可能になっています」と説明するのは、中央発條 システム企画室 IT化推進G 森田 夏紀氏だ。
従来は、工場の生産管理部門が毎朝在庫数をカウントし、Excelに集約するという作業を1~2時間をかけて行っていたという。現在は、在庫を保管する箱に添付された現品票のQRコードから品番と収容数を読み取ることでDb2に反映。システム上の在庫数として表示される。今後は他の工場についても手作業による在庫のカウントを廃止し、在庫管理は全てGalleriaSoloで表示する予定だという。
一方の、売上管理については、シャシばねや精密ばね、コントロールケーブルの主要製品のほか、ばね部品を単体で販売するケースや、海外の関係会社に材料を供給するケースなどがある。それらをドリルダウンで得意先別・品番別に日次の売上を可視化し、簡単でわかりやすい運用を実現している。
「月初の売上予測と月末の売上結果とで差異が生じた場合に、品種別・得意先別に原因を調べるための第1ステップとしてGalleriaSoloを活用しています。今までは時間をかけてデータを直接見て調べていましたが、導入後はその作業が格段に効率化しています」と想厨子氏は述べる。営業担当者全員がGalleriaSoloを毎日確認するようになったことで、デリバリーや納期調整に向いていた意識を日々の売上の変化にも向けられるようになり、品種ごとの需要の変化を細かく意識するようになったという。
現在の運用と評価
これまで見えなかったものを見える化し 労力をかけていた見える化も簡単に実現
GalleriaSolo 導入によって、主に3つのポイントが見えてきたという。1つ目は、従来見えなかったものが見える化したこと。この変化について森田氏は、「これまで製造現場ではリアルタイムでの在庫数を把握する手段がなかったため、時間ごとの在庫数の変動については比較的関心が薄かったのですが、リアルな数字をグラフなどで掲示し、一元的に状況を把握できるようになってからは、グラフに示された数字の意味についての問い合わせや、在庫が不足しそうなアイテムを指摘するケースが増えるなど、現状に対する意識が変わったように感じます」と分析する。
2つ目は、労力をかけて見える化していたものを簡単に見える化ができるようになったこと。製造現場の担当者がExcelで作っていた手間や時間を大幅に削減し、本来の業務に集中するようになったことで、例えば在庫不足分の追加生産を生産管理部門に依頼するアクションも迅速にとれるようになったという。
3つ目は、Excelとの住み分けが明確になったこと。想厨子氏は「GalleriaSoloを単純にExcelからの置き換えで活用するわけではありません」という。Excelにはグラフのスタイルを変えたり、コメントを加えたり、予算と実績を対比させたりすることが手元で簡単にできる手軽さがある。一方のGalleriaSoloは、今まで見ていなかった情報がすぐにグラフ化できるほか、例えば欠品する恐れのあるアイテムや品番が発生すると点滅によるアラートが出せるので、何か起きているという意識付けに効果的だという。
今後の展望
GalleriaSoloで製造に必要な時間を短縮し 総労働時間の短縮にも取り組む
中央発條では、今後GalleriaSoloを各工場にも展開していくほか、未使用・未利用部門への活用も促進していく考えだ。また、全社で総労働時間の短縮にも取り組む意向を示しており、お客様の内示から見込みの工数を積み上げ、その予想作業時間と実際の作業時間との差異をGalleriaSoloで可視化することで、製造に必要な時間の短縮をめざしていくという。
今回のGalleriaSolo導入を振り返り、森田氏は「見える化を進める会社の取り組みに自分も参加できたことはとてもうれしく思います。GalleriaSoloは一度操作を覚えれば運用は簡単なので、BIダッシュボードのハードルは決して高くはないと感じています」と話す。
そして想厨子氏は、「ようやくデータ活用のスタートラインに立つことができたので、今後はこれをいかに活用していくかが問われます。そのためにも、GalleriaSoloの使い方をマスターするスタッフを増やし、生産性を高めていきたいと考えています」と語る。
現代の自動車には数千点ものばねが使われているといわれ、今後電動化や自動化が進んでもその必要性や重要性は失われることはない。中央発條の弛まぬ革新と創造を今後もDTSとGalleriaSoloは支え続ける。